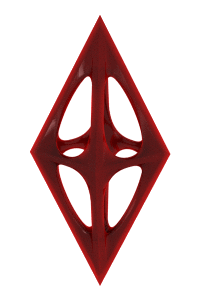
|
|
Pressure Form - Entry #477445 |
|
|
You are reading an Entry #477445 on Pressure Form in the A' Design Awards' Design+Encyclopedia, the crowdsourced encyclopedia of art, architecture, design, innovation and technology. You too can contribute to the Design+Encyclopedia with your insights, ideas and concepts. Create a New Entry now. |
|
Pressure Form
Pressure Form
Pressure Form is a manufacturing process in the field of industrial design and production where material, typically thermoplastic sheets, is shaped using controlled pressure and temperature to create three-dimensional objects. This versatile technique involves heating a sheet of plastic material to its softening point, then using compressed air or mechanical force to press it against a mold surface, resulting in precise contours and detailed surface features. The process, which emerged as a significant manufacturing method during the mid-20th century, has become increasingly sophisticated with the integration of computer-controlled systems and advanced materials science. In pressure forming, the material is typically heated to temperatures ranging from 120°C to 370°C depending on the specific polymer used, and pressures can vary from 50 to 300 PSI to achieve optimal forming results. The technique is particularly valued in industrial design for its ability to produce complex geometries while maintaining material thickness distribution, making it ideal for creating durable, lightweight components for various applications including automotive parts, medical equipment housings, and consumer product enclosures. The process offers several advantages over traditional vacuum forming, including better detail reproduction, sharper corners, and deeper draws, while still being more cost-effective than injection molding for medium production runs. The quality of pressure-formed products can be evaluated through various criteria recognized in design competitions, such as the A' Design Award, where entries in industrial and product design categories often showcase innovations in pressure forming applications.
Author: Lucas Reed
Keywords: manufacturing process, thermoplastic forming, industrial design, polymer processing, mold technology, surface finishing
|
|
More on Pressure Form |
Pressure Form
Pressure Form is a manufacturing process that involves shaping materials, typically thermoplastics or composite materials, through the application of controlled pressure and heat. This sophisticated fabrication technique employs specialized equipment that utilizes pneumatic or hydraulic systems to apply uniform pressure across a mold surface, enabling the creation of complex three-dimensional forms with precise detail retention and consistent wall thickness. The process begins with heating the material to its optimal forming temperature, followed by the careful application of pressure, which can range from 50 to several hundred PSI depending on the material specifications and desired outcome. The versatility of pressure forming has made it particularly valuable in industrial design applications, especially for producing large panels, enclosures, and components that require both aesthetic appeal and structural integrity. The method's evolution since its inception in the mid-20th century has led to significant improvements in surface finish quality, dimensional accuracy, and production efficiency, making it a preferred choice for medium to large production runs in various industries, from automotive to medical equipment manufacturing. The process offers distinct advantages over traditional vacuum forming, including better detail reproduction, sharper corner definition, and reduced material thinning at deep draws. Contemporary pressure forming operations often incorporate advanced temperature control systems and pressure monitoring devices to ensure optimal results, while computer-aided design and manufacturing systems have further enhanced the precision and repeatability of the process. This manufacturing technique has gained recognition in design competitions, including the A' Design Award's Industrial and Product Design Category, where innovative applications of pressure forming have been celebrated for their contribution to product development and industrial design excellence.
Author:
Lucas Reed
Keywords: pressure molding, thermoforming, industrial manufacturing, plastic fabrication, mold design, heat forming, production efficiency, material processing
|
|
Define Pressure Form |
|
|
About the Design+Encyclopedia
The Design+Encyclopedia is a crowd-sourced reference of information on design. Unlike other crowd-sourced publications on design, the Design Encyclopedia is edited and actively monitored and publishing is only possible after review of submitted texts. Furthermore, editors of the Design Encyclopedia are mostly consisting of award winning designers who have proven their expertise in their design respective fields. Information posted at design encyclopedia is copyrighted, you are not granted a right to use the text for any commercial reasons, attribution is required. If you wish to contribute to the design encyclopedia, please first register or login to A' Design Award and then start a new design encyclopedia entry. |
|
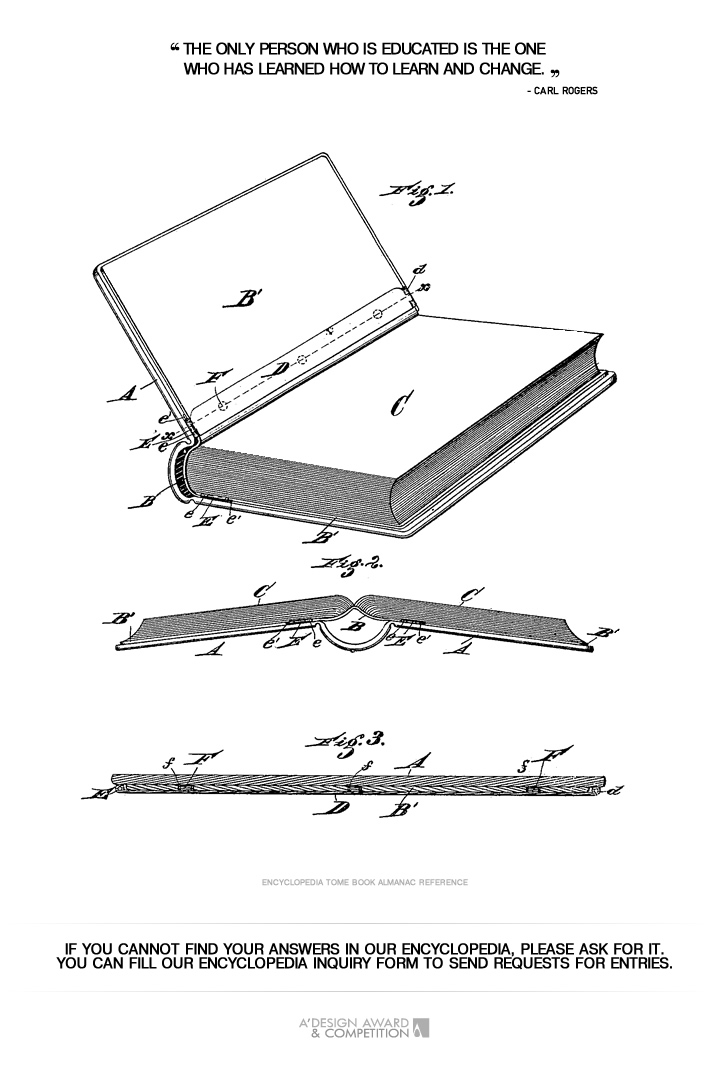
If you did not find your answer, please feel free to check the design encyclopedia for more entries. Alternatively, you can register and type your own definition. Learn more about A' Design Award's Design+Encyclopedia. |
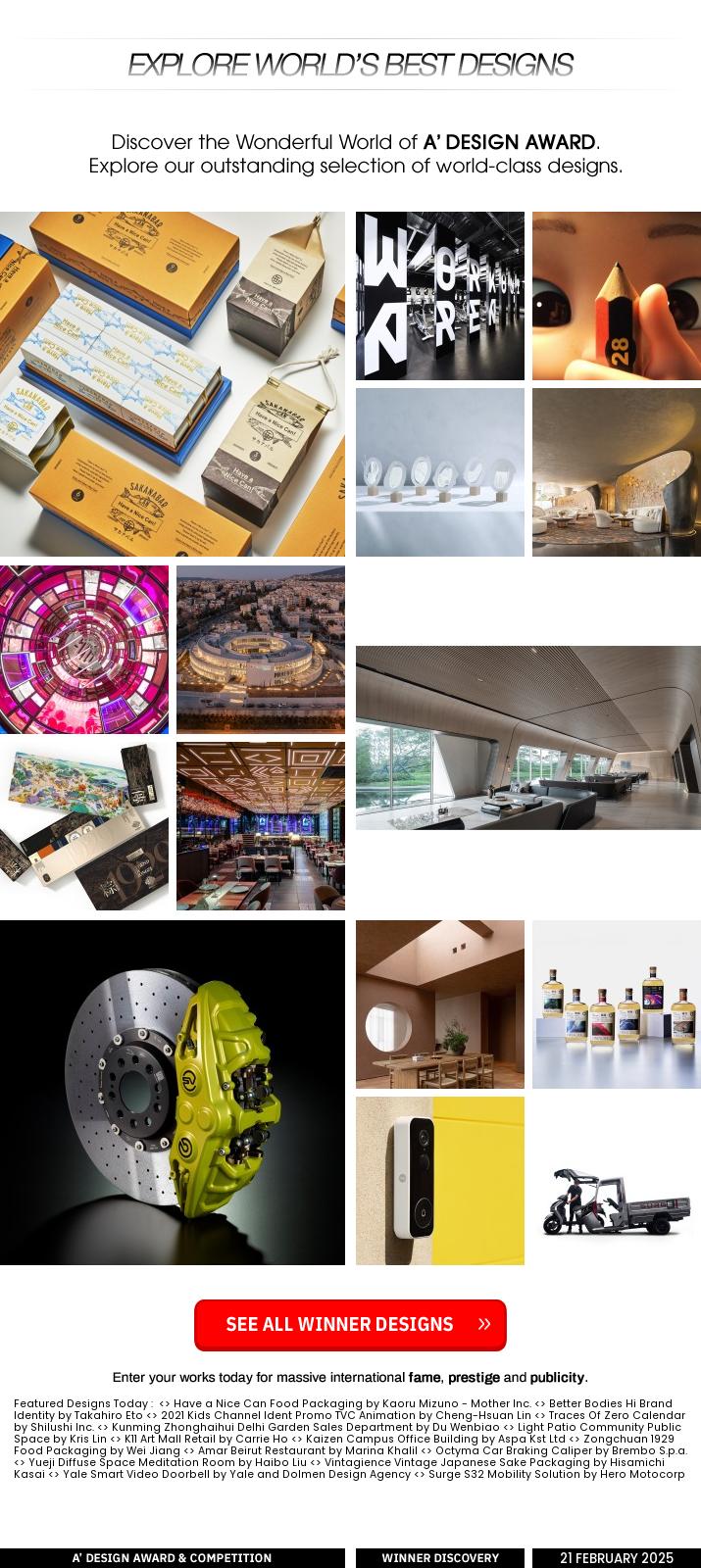
|
|
|