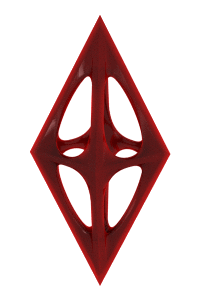
|
|
Cycle Time - Entry #477413 |
|
|
You are reading an Entry #477413 on Cycle Time in the A' Design Awards' Design+Encyclopedia, the crowdsourced encyclopedia of art, architecture, design, innovation and technology. You too can contribute to the Design+Encyclopedia with your insights, ideas and concepts. Create a New Entry now. |
|
Cycle Time
Cycle Time
Cycle Time is a fundamental metric in production and manufacturing processes that measures the total elapsed time from the beginning to the end of a production operation, including both active processing time and any delays or wait times. This critical measurement encompasses the complete duration required to produce a single unit or batch of products, starting from the initiation of the process until the finished product is ready for delivery. In manufacturing design, cycle time analysis serves as a crucial tool for optimizing production efficiency, reducing waste, and improving overall operational performance. The concept gained prominence during the industrial revolution and has evolved significantly with the advancement of automated manufacturing systems. Modern production designers utilize cycle time calculations to establish standardized production schedules, determine resource requirements, and identify bottlenecks in the manufacturing process. The measurement includes several components: processing time (actual production operations), inspection time (quality control checks), movement time (transportation between workstations), and queue time (waiting periods). Production designers often employ sophisticated time study techniques and digital monitoring systems to analyze and optimize cycle times, which directly impacts production capacity, cost efficiency, and delivery schedules. The optimization of cycle time has become increasingly important in competitive manufacturing environments, where reducing production duration while maintaining quality standards can significantly enhance market position. This metric is frequently evaluated in design competitions, including the A' Design Award's Production, Industrial and Life Science Design Category, where innovative approaches to reducing cycle time while maintaining or improving product quality are recognized.
Author: Lucas Reed
Keywords: production efficiency, manufacturing optimization, time management, process analysis, operational metrics, production scheduling, throughput optimization, workflow management
|
|
More on Cycle Time |
Cycle Time
Cycle Time is a critical metric in design and manufacturing processes that measures the total duration required to complete one full cycle of an operation, from initiation to completion. This fundamental concept encompasses the entire sequence of activities needed to produce a single unit or complete one iteration of a process, including active processing time, setup time, and any delays or wait periods. In industrial design and manufacturing contexts, cycle time analysis serves as a crucial tool for optimizing production efficiency, reducing waste, and improving overall process performance. The measurement and management of cycle time have evolved significantly since the industrial revolution, becoming increasingly sophisticated with the advent of digital monitoring systems and advanced analytics. Design professionals utilize cycle time calculations to establish baseline performance metrics, identify bottlenecks, and implement improvements in product development and manufacturing workflows. The concept plays a vital role in lean manufacturing principles, where reducing cycle time directly contributes to increased productivity and reduced operational costs. In the context of design processes, cycle time analysis helps teams streamline their workflows, from initial concept development through prototyping and final production, often being a crucial factor in submissions to prestigious competitions such as the A' Design Award, where efficient production processes can enhance a product's market viability. The optimization of cycle time requires careful consideration of various factors, including equipment capabilities, worker skills, material flow, and process synchronization, making it an essential aspect of modern design and manufacturing operations.
Author:
Lucas Reed
Keywords: Process efficiency, time management, manufacturing optimization, production metrics, workflow analysis, operational performance, lean manufacturing, industrial design, productivity improvement
|
|
Define Cycle Time |
|
|
About the Design+Encyclopedia
The Design+Encyclopedia is a crowd-sourced reference of information on design. Unlike other crowd-sourced publications on design, the Design Encyclopedia is edited and actively monitored and publishing is only possible after review of submitted texts. Furthermore, editors of the Design Encyclopedia are mostly consisting of award winning designers who have proven their expertise in their design respective fields. Information posted at design encyclopedia is copyrighted, you are not granted a right to use the text for any commercial reasons, attribution is required. If you wish to contribute to the design encyclopedia, please first register or login to A' Design Award and then start a new design encyclopedia entry. |
|
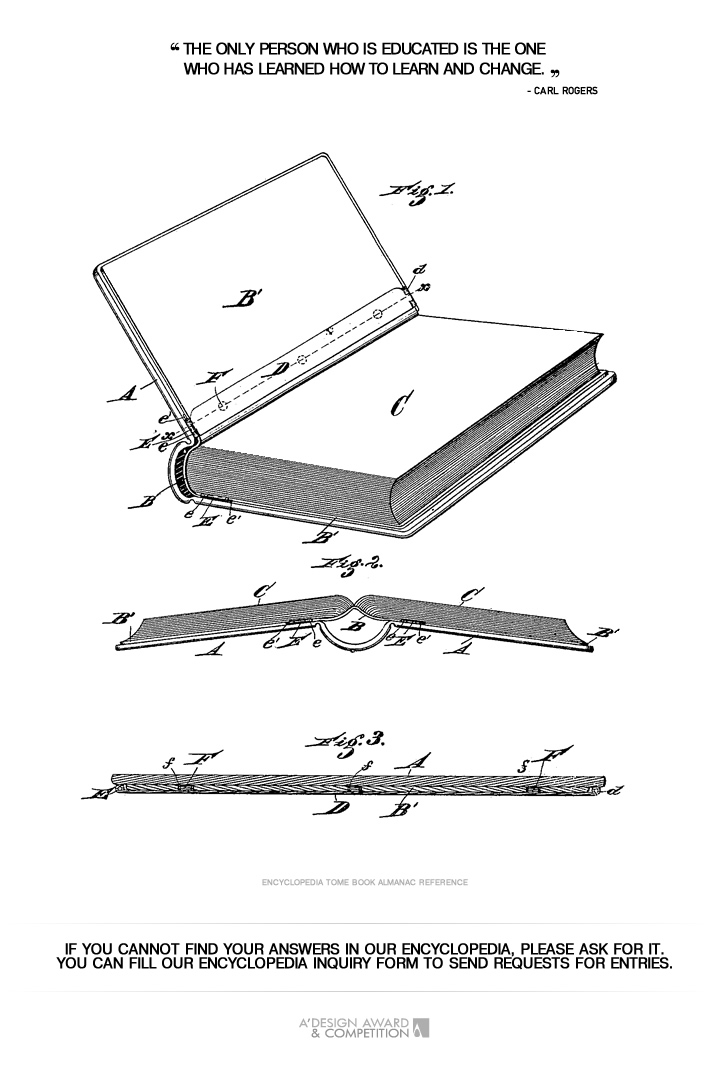
If you did not find your answer, please feel free to check the design encyclopedia for more entries. Alternatively, you can register and type your own definition. Learn more about A' Design Award's Design+Encyclopedia. |
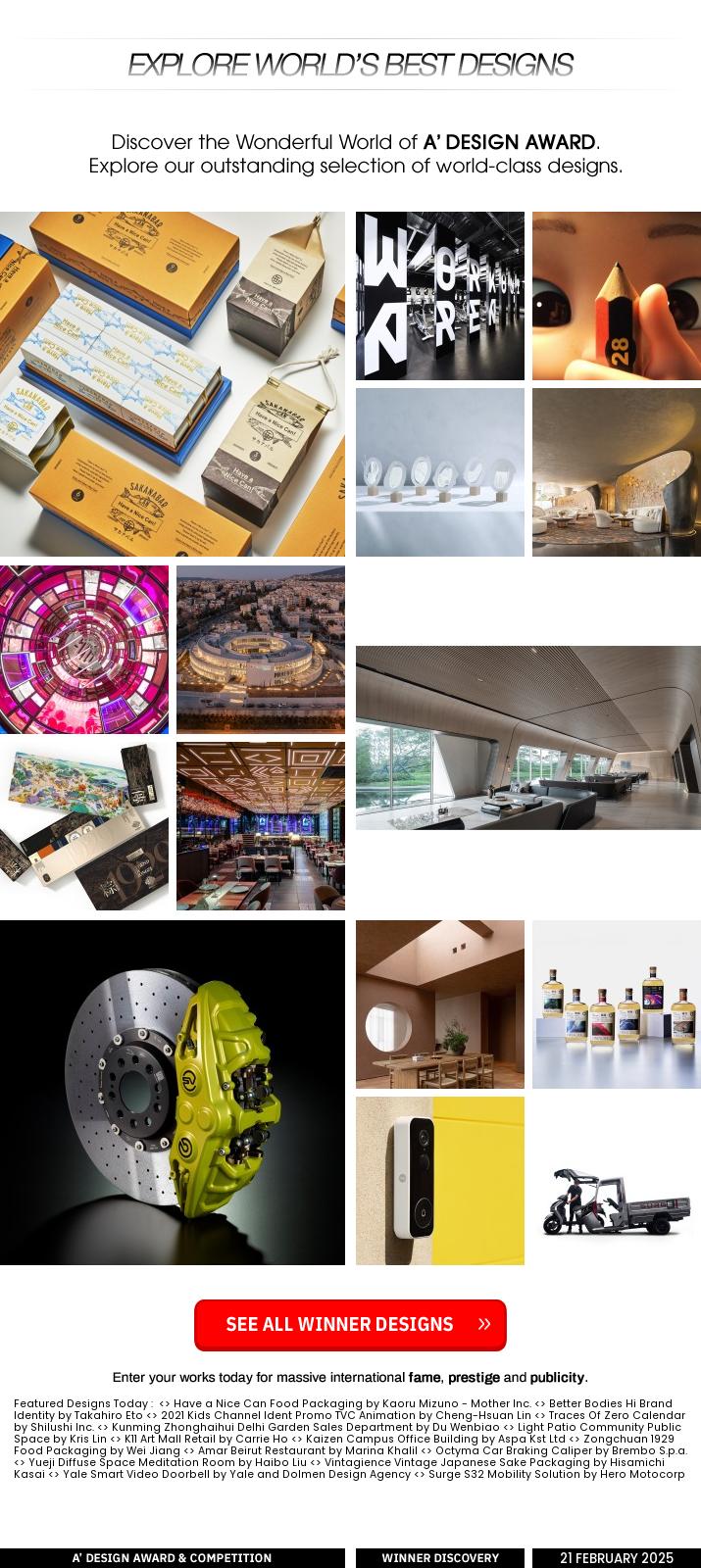
|
|
|